Kitekraft enters into a new phase towards building commercially available flying wind turbines. After laying the ground work with research at the Technical University of Munich and continuing with extensive prototyping after spinning out into Kitekraft, we are excited to present our new, fully integrated prototype, bringing together kite and ground station. After several iterations and extensive integration testing, the system is now operating as one unit, capable of all operations our commercial product will perform. This system is now a fully functional test platform for our further development as our focus shifts from the conceptual work towards improving reliability and efficiency instead. This represents a step change in our ability to test and fly our kites, greatly accelerating our development.
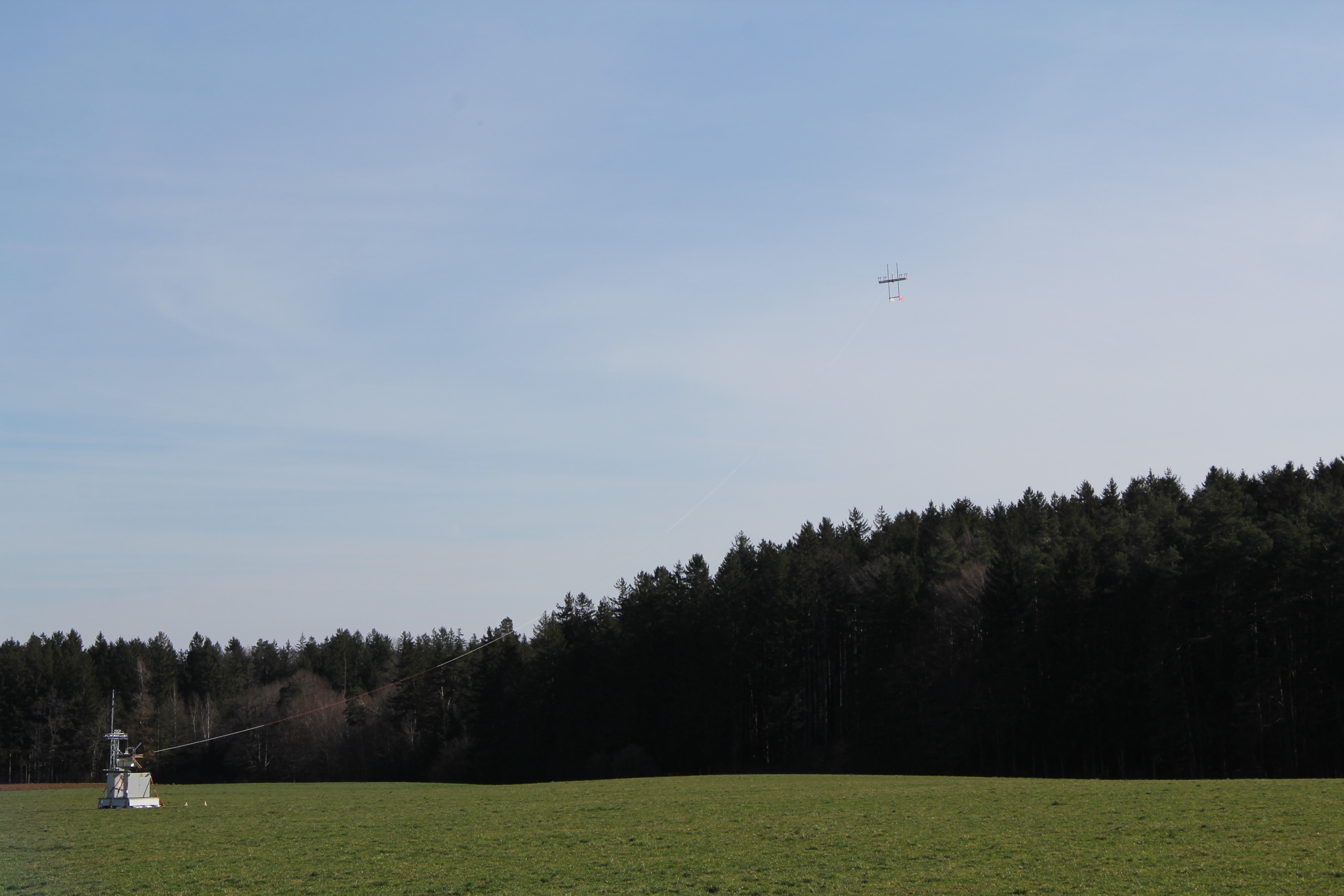
This new status comes after two months which have been the most successful in Kitekraft’s development ever. We completed several successful test days with separate flights of varying length. All these tests were performed over the full operational envelope and with our fully integrated system of ground station, tether and kite. As has been standard for quite sometime, all tests were executed autonomously by our proprietary software with just highest-level commands (like “start into hover”, “start into figure-eight flight”), and specific controller changes, as part of the test regime, being given “by hand.” All recent flights were stopped on our own terms and only out of precautions to review flight and system data.
Flight phases within all tests included the following operational phases as they would also be seen in every product version.
- VTOL take-off from the ground station perch.
- Hovering away from the ground station while reeling out the tether to its full extension.
- Rotating landing perch to the back.
- Transition into the figure-eight flight.
- Figure-eight flight.
- Transition out of the figure-eight flight to hover.
- Rotating landing perch to front, catching the tether.
- Reeling in the tether.
- VTOL landing.
This brings together different development efforts over the last years. We have already been flying our kite in figure-eight flight for a while. This was done though without a functional ground station and instead with something you could rather describe as a ground anchor. Since we had no winch, we needed to start with an extended tether from the field. Nonetheless, we were able to demonstrate stable flight and prove kite design, aerodynamics, power- and microelectronics as well as the control systems. On a separate track we had already developed first versions of the ground station and tested indoor take-off and landing. Those tests led to several design iterations and finally to the current ground station prototype with which we could start integration testing of the full system in the summer of last year. In fall we completed the first crosswind flight with all steps of the ground station. By March this year we integrated waterproof cabinets and lots of redundancies to the ground station and were able to fly as planned.
Reaching this development step is crucial and brings us much closer to developing a first commercially available system. Commercial viability is closely tied to flight hours and operational experience. To properly develop airborne wind energy systems, make them safe, reliable and efficient, the system needs be understood and tested in its entirety. Flying more is the way to go. It is not just needed for the development though, flying more helps to de-risk the technology for our customers, regulators, insurers as well as financing partners. All is needed to let this technology take off. Our fully integrated prototype is the enabler for exactly that, flying more, improving controls, increasing reliability, and ensuring efficiency.
The technical achievements are accompanied and enabled by our fundraise last year which led to a doubling of team size and allowed us to move into our new office and workshop at the beginning of the year. In the coming months we will push our system to its boundaries while continuously implement improvements. This includes further redundancies, control system updates, testing and implementation of new and efficient rotors, connecting our current test site to the grid and improving our simulation environment. These steps lead towards the upscaling of the prototype, doubling the wingspan to 5m, with which we significantly increase the system’s efficiency and proof the system’s power curves.
We are excited for what is to come. Onwards and upwards!